Manually collecting vibration data once a month with a data collector does not always provide enough information for proper analysis of equipment problems. In many cases, the problem doesn’t occur when the technician takes a vibration reading, or the amount of data is not sufficient for detecting problematic trends.
Using a remote monitoring solution to collect more frequent data for analysis can greatly improve the success of a predictive maintenance program and enable analysts to catch problems before consequential damage occurs.
Why Once-A-Month Data Collection Became the Norm
The introduction of handheld data collectors in the 1980s was a turning point for continuous process plants. These new programmable “black boxes” enabled teams to collect vibration data along a predetermined route and then download it to a computer for analysis. Used primarily for rotating machinery, handheld data collectors significantly expanded predictive maintenance capabilities and complimented the fault protection systems already in place.
As data collector use spread among industries, maintenance professionals quickly found that monthly data collection made the most sense. This realization was primarily due to the sheer size of plants and the time it took for data to be collected. For example, a typical steel mini mill with a cold mill has 500 to 600 machines in need of monitoring. On average, analysts would need at least five data points from each machine. That meant they would need to collect at least 2,500 data points to survey an entire plant.
In addition, other factors impacted the time it took to collect data:
- Magnitude and layout of the plant. Some plants are made up of multiple buildings, spread out in a campus-like setting.
- Security. Security procedures, such as those at nuclear plants, require all personnel be cleared to get in and out of the plant.
- Physical location. Some critical machines are in hard-to-reach locations or require safety precautions be taken before accessing.
Surveying an entire plant with a single data collector often takes more than a week — and that is just the collection phase. After that is data analysis, which is a whole separate process.
As the use of handheld data collectors became industry standard, most plants instituted monthly rounds. For most, monthly collection not only made the most sense in regards to timing, but was also the most cost effective, as longer collection times meant higher labor costs.
Limitations of Monthly Data Collection
Monthly manual data collection and analysis will catch most slow-developing degradation issues that typically occur on rotating equipment that runs continuously. This includes bearing failures, alignment issues, and looseness, for example. However, there are several drawbacks to monthly manual data collection:
- Snapshot in nature. Monthly data, even years of it, may not reflect the actual operating condition of a machine. Important day-to-day variations may be missed.
- Not enough data for diagnosing multiple root causes. When a complex equipment problem occurs as a result of multiple root causes, monthly data collection almost never provides enough information for even the most skilled of analysts to diagnose.
- Rarely catches rapidly developing problems. Equipment issues that develop quickly often go undetected until the situation is critical because they occur in between collections.
- Not all equipment runs continuously. Some machinery may only run once a quarter, or on an as-needed basis. The day a technician collects data from that machine may not be a day the machine is running. More often than not, operation personnel will not run a machine just for the sake of data collection.
- Not all equipment is run at one speed. Variable speed motors can change operating speed daily or hourly. Other machines may run differently depending on the environment (such as day vs. night). Monthly data delivers little information for analyzing these types of machines.
- Problems often happen at inconvenient times. Thanks to Murphy’s Law, equipment problems often happen during nights, weekends, and holidays when no one is taking data.
Traditional manual data collection also falls short when a machine starts acting up but cannot be taken out of service. Closely monitoring a problematic machine to an outage requires more frequent data collection (weekly or even daily).
For plants with a monthly walk-around route, the only option is to have someone constantly monitor the ailing machine. Labor costs associated with more frequent data collection are astronomical, especially for plants whose data collection and analysis are done by a third party. These callouts are charged at a premium.
Regardless of the cost, manual collection may still fall short because collecting enough data at the right time and from the right locations can be near impossible — even with a skilled analyst camping out around-the-clock.
The Impact of Not Catching Impending Failures
One of the main reasons for having a machine monitoring program is to mitigate impending failures. Monitoring the overall health of assets in a plant helps ensure that signs of impending failures are properly identified so that appropriate actions can be taken in a controlled and timely matter to maximize equipment availability. The cost of not being able to control equipment downtime can be astronomical.
Taking a piece of equipment down suddenly for repair/replacement not only costs a premium in labor expenses, but can also result in massive production losses. For example, a power plant with reduced capacity due to an equipment problem may need to buy power on the open market during peak usage to meet the needs of its customers. Or for a steel manufacturer, it could mean not meeting contractual obligations on the delivery of product.
In addition, not detecting an impending failure could result in damage to surrounding equipment. These consequential damages increase the amount of labor needed to repair/replace equipment and ultimately drive up operating costs.
The availability of spare parts must also be factored into the cost of sudden failure. Plants don’t often carry spare parts in-house for all pieces of equipment. Therefore, parts may need to be tracked down from suppliers on short notice. Depending on the type of parts, significant expedite fees may be charged for both the actual part and rush shipping.
Benefits of Automated Monitoring
Automated data collection enables plants to overcome many of the issues faced by manual data collection programs. By increasing the frequency of collection, analysts are able to get a better picture of the actual operating condition of a machine and can more easily detect rapidly developing problems.
These systems also enable analysts to schedule collection around equipment service and often enough to catch data at different speeds on variable speed motors. The ability to collect vast amounts of data also gives analysts the tools they need to solve problems with multiple root causes. In addition, automated systems can collect data around-the-clock, including nights, weekends, and holidays.
Remote monitoring also helps plants deal with the growing skills shortage facing continuous processing industries. With few new analysts coming up the ranks, a high rate of retirement, layoffs, reorganizations and other factors are taking their toll on predictive maintenance programs. Today’s connected systems let analysts cover more industrial real estate and share data with others to get advice, determine root causes, and make better, more informed judgment calls. These systems also allow analysts to share data with the equipment manufacturer or an outsourced maintenance company that may have performed the last overhaul on a piece of suspect machinery.
With monthly manual monitoring, teams spend a significant amount of time physically gathering data. In most cases, analysis does not even begin until the route is complete — which could be days or even weeks later. Automating data collection allows the analysts to focus on gathering insights rather than the physical data collection, which boosts efficiency.
Personnel safety is another obstacle that automated monitoring addresses. Equipment in dangerous areas or in locations that require protective gear (for example, harnesses or respirators) can now be monitored without the risk of injury.
Integrating Automated and Manual Data Collection
While some plants may opt to go the automated route for all of its monitored machines, others may want to marry the two types of collection to create a customized predictive maintenance program.
By using software like a computerized maintenance management system (CMMS) that integrates data from multiple sources, teams can view data collected manually and automatically through a single platform. The CMMS then allows the plant’s staff or an outside analyst to review the data. Such systems enable plants to combine the two types of collection to their advantage by applying the collection method that best suits each particular machine.
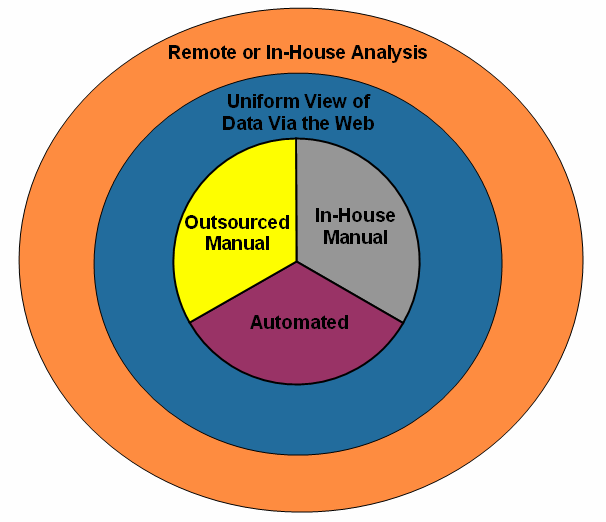
Fig. 1: Delivering a uniform view of equipment health
Equipment that is critical to production or has a history of problems would be monitored with the automated system. This ensures they are watched frequently around the clock. Less critical equipment would be monitored manually using the traditional monthly route. Integrated systems often include mobile devices that can be moved quickly from one machine to another. This is helpful when a machine under monthly surveillance becomes problematic and requires more intense monitoring for diagnosis.
Case Studies
The following case studies demonstrate specific instances where daily data collection by a remote monitoring system enabled Azima’s vibration analysts to detect problems well before consequential damage occurred. (Azima’s analysts are ISO trained Level II-IV and provide diagnostics on more than 500,000 machine tests a year. Equipped with Azima’s advanced AI, they are 5x more efficient than traditional analysts. Click here to learn more).
These catches would not have been possible with standard monthly data collection.
Case Study 1: Multiple Root Causes Plague Forced Draft (FD)
Fan One of two critical FD fans at a MCGS 469-megawatt power plant had historically exhibited higher levels of vibration than its counterpart. However, following an outage, the problematic fan displayed radial levels that were just too high to ignore. Because the fan was critical to production, it could not be taken out of service. To closely monitor the fan, the plant’s reliability manager deployed a mobile remote monitoring system within an hour and had the system collect vibration data every hour around the clock.
A few days later, just after 3 a.m., the monitoring system detected a substantial step increase on the fan inboard bearing and a drop on the outboard bearing. (Azima’s diagnostic engine has been trained on 30 years of data, drawing from 100 trillion data points across 50 machinery component types – surpassing competitors in the market. This large dataset enables AI systems to understand and navigate numerous machine variations and real-world scenarios. Click here for more info).
The following figures show the increase and decrease, as detected by the remote monitoring system.
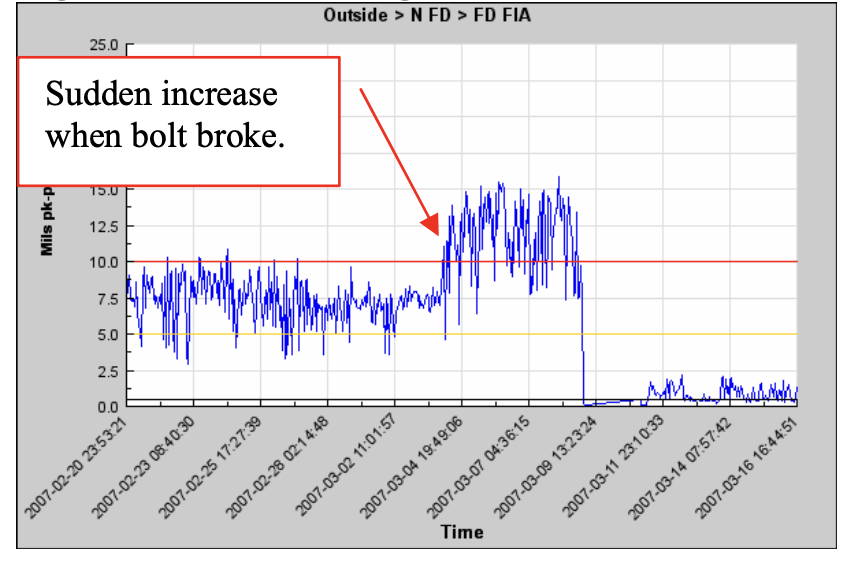
Fig. 2: Outboard Bearing Trend

Fig. 3: Inboard Bearing Trend
Because the plant’s connected monitoring system generates automated alerts based on predetermined thresholds, the off-site, on-call analyst was notified and able to look at the data remotely. The analyst determined that the outboard bearing plunger bolt had most likely come loose and quickly alerted plan management. Moving fast enabled the team to schedule time to take down the fan, rather than be forced into an emergency repair situation.
Because of the vast amount of data collected from multiple points on the fan, the analyst was able to determine exactly where to start troubleshooting. This decreased the amount of time needed to find the root cause. In this case, the evidence pointed to three separate root causes:
- The plunger bolt on the outboard bearing came loose. The bolt was supposed to have 104 lb-ft of torque. Upon inspection it was identified that the bolt had no torque and was a quarter turn loose.
- The right front pedestal base plate was moving relative to the grout. When technicians attempted to tighten the bolt, they discovered that it was broken and the nut was just sitting on top of the broken bolt. The sudden increase in level shown in Figure 3 was likely caused when the bolt failed completely. Sudden increases, like those in Figure 2 and Figure 3, cannot be detected by once-a-month snapshots. As a temporary fix, another bolt was welded to the broken stud. After doing this, the monitoring system detected that the vibration levels had dropped — but not as much as expected.
- Significant rotor imbalance. Once the bolts were tightened with the appropriate amount of torque and the pedestal base plate fixed temporarily, technicians noted that the rotor was out of balance.
After all three issues were resolved, the fan’s vibration was much closer to that of its sister fan. The loose pedestal plate may have been an issue for a long time and appears to explain why the fan had a history of vibration problems.
This case study illustrates how a remote monitoring system can enable an analyst to solve complex issues with multiple causes quickly — before consequential damage occurs. This is not possible with traditional manual data collection. In addition, the analyst was able to review data and make recommendations remotely, thus saving the plant the cost of repetitive call-outs.
Case Study 2: Rapid Deterioration Puts Induced Draft (ID) Fan in Jeopardy
Technicians replaced an ailing motor in an induced draft (ID) fan on a hot strip mini mill with a reconditioned one. Though the fan appeared to be running fine after the replacement, the remote monitoring and diagnostic system in place immediately detected high vibration levels at start-up. The remote monitoring system sent an automated alert to the mill’s on-call analyst, who reviewed the data. An initial look at the spectral data indicated a problem with the ID motor bearing, as shown in Figure 4.
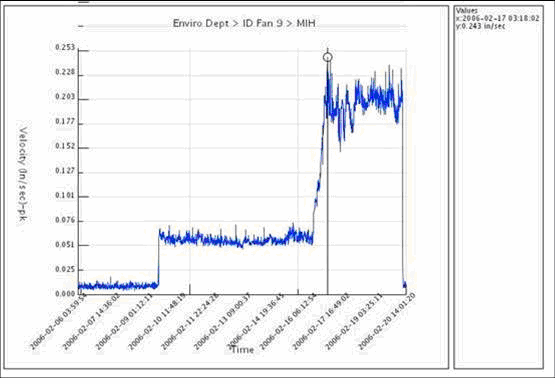
Fig. 4: Vibration increase on ID motor bearing
Using the system’s connected diagnostic tools, the analyst — who was 300 miles away — performed a more detailed analysis. He determined that there was an outer race fault on the motor inboard bearing. The defect was not severe enough to force an immediate shut down and, at the current rate of degradation, the analyst felt the fan would make it to a scheduled outage a few weeks away.
However, just two days later, the situation changed when a mill maintenance worker mistakenly added specialty grease to the motor. Within hours, the monitoring system detected an accelerated degradation of the bearing (see Figure 4).
The analyst was again notified by the system and he immediately contacted the mill’s environmental manager. With vibration levels climbing, it was clear to the analyst that the motor was in danger of immediate failure. The mill decided to swap out the ID fan with a spare one.
To avoid a repeat of the problem, the spare fan was connected to the remote monitoring system and watched for a short period before being put into service. The swap was made without any impact on production.
This case study shows how Azima’s remote condition monitoring solution can detect rapidly developing problems, giving plant personnel a chance to decide on remedial action before failure or consequential damage occurs. By detecting the issues with the ID fan early, the plant was able to make controlled decisions about the replacement and repair. Had the fan been on a monthly walk-around route, there is little chance that either the initial vibration increase or the rapid deterioration after the lubrication was added would have fallen at the same time as the data collection.
In addition, the mill did not have to pay for the analyst to investigate the problem in-person. All data analysis was done remotely, without a single site visit.
Case Study 3: Circulating Water Pump Develops Problems During Hottest Time of the Year
Circulating water pumps are extremely important pieces of equipment to a power generating station because they supply cooling water to the condenser. If there is not enough water supplied to the condenser, the back pressure increases and can destroy the low-pressure turbine blades. If the back pressure increases as a result of low water flow, it is then necessary to reduce the output of the turbine, leading to decreased revenue.
After an 800-megawatt nuclear power plant overhauled one of its circulating water pumps, vibration levels were noticeably higher. Since the weather was still warm, the pump was necessary to ensure that the turbine could be kept at full load. In an effort to make both operations and executive management comfortable with the continued operation of the pump, technicians installed an automated monitoring system. Alarm thresholds were set up to notify both operations and the plant’s analysts if the level surpassed a predetermined value.
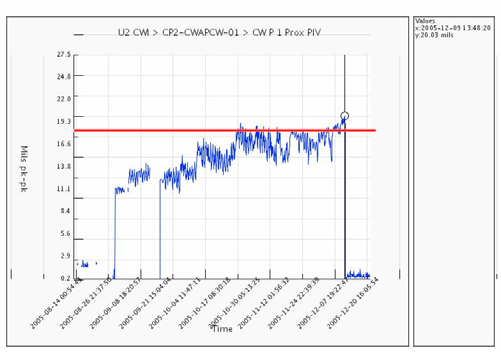
Fig 5: Trend of inboard proximity probe showing alert threshold
The system monitored vibration levels around the clock until the weather was cool enough to allow the pump to go out of service without derating the plant. Upon inspection, plant personnel discovered that a previous repair (which happened in an emergency situation) was completed incorrectly. A critical clearance had been set improperly, thus resulting in the increased vibration.
This case study shows how a remote monitoring system can keep an eye on a piece of equipment to extend its run time so plant personnel can take it down on their terms. Without the automated monitoring system, plant personnel would have had to manually collect data on the pump for several months. This would have been extremely time consuming and costly. Monthly data collection in this case was simply not sufficient enough to adequately monitor the health of the pump to ensure the safe operation into the cooler months.
By extending the run time of the pump until cooler weather, the team could make repairs in a controlled, non-emergency environment.
Author bio:
Heather De Jesús is the Systems Engineer Manager at Azima and a Level II Vibration Analyst.