Correct diagnosis of rotating machinery faults relies on complete information about vibration spectral data. Since machines generally have three degrees of freedom of lateral motion, good science and logic suggest that data from all three axes will provide more information if we can analyze it properly.
In this article, we’ll demonstrate the improved diagnostic capability provided by collecting triaxial data compared to single-axis radial data mixed with some axial data.
What Are the Three Orthogonal Axes?
The three orthogonal axes are the different directions that a sensor can collect data. Triaxial sensors monitor all three axles: axial, radial, and tangential. As indicated by the term, the axial is the direction in line with, or parallel to, the shaft. Radial and tangential are the two perpendicular axes in the plane of rotation.
Three single-axis accelerometers are incorporated into a small cast bronze cluster block with a threaded pin. Bronze disks, with a threaded hole to accommodate the cluster pin, attached with adhesives to bare metal surfaces at selected transducer locations. These disks remain indefinitely unless a maintenance team makes a special effort to remove them. Often these sensors are placed on bearing housings or on stiff portions of structure that are physically close and have a direct vibration path to the bearing housings.
Generally, triaxial spectral data is collected at one or two transducer locations on each major component of a machine. The decision of whether to use one location or two usually is dependent on the size of the machine. The data quality and frequency range are comparable to permanently installed transducers.
How Does Triaxial Data Collection Work
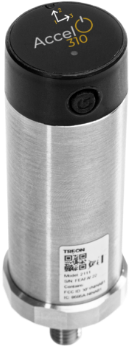
Accel 310 – Triaxial sensor by AzimaDLI
Modern hardware has made data collection easier than ever. Today’s triaxial solutions can be deployed as permanently mounted wireless sensors, as a portable data collector, or collected as part of a permanently installed online system.
The total time required to capture all three axes is a function of the monitored shaft speed as well as the capability of the hardware to capture three channels simultaneously or in series. In general, slower speed shafts require more time to sufficiently capture the vibration signature. Systems that process channels in series, such as the wireless sensor, also take longer to capture.
After the data has been collected, it is transported off the device and into a location for software and specialists to analyze the spectra. Data processing includes order normalizing the spectra (changing the frequency scale to reflect multiples of the machine rotating speed), screening the spectra to obtain significant spectral peaks, and performing automatic diagnosis to determine specific machine faults and their severities.
Using all three axes of data per location, information from a typical machine can be processed in about 30 seconds, depending on the number of transducer locations. The philosophy of using triaxial data is independent of software and may be used with any method of fault diagnosis.
Detecting Machine Faults With Vibration Data
Although software can accommodate vibration displacement, velocity, or acceleration in any unit of measurement, we generally measure machinery velocity vibration in velocity decibels (VdB), which is a log scale referencing 0 VdB = 10-8 meters per second RMS. For the sake of perspective, 0.1 inch per second peak vibration is equal to 125.1 VdB. A 6 VdB differential is linearly a factor of two and 20 VdB is linearly a factor of ten.
The spectral amplitudes of vibration are compared to average baseline data accumulated for a specific machine type. (With a hundred trillion data points stored in its data lake, Azima’s AI-powered diagnostic engine can diagnose 1200 asset and component faults. The tool also continues to learn and improve its diagnostic capabilities the longer it operates).
The levels used are average plus one standard deviation values statistically computed for each spectral peak from selected past test data for the machine type. When we refer to the relationship of an amplitude to average, we mean average plus sigma (= 1 standard deviation). Fault severities are designated “slight”, “moderate”, “serious,” and “extreme”.
Azima’s analytical software computes the severity based on the margin by which the various test amplitudes and exceedances of average plus sigma compared to the threshold values as required for the specific fault diagnosis. Table 1 presents this information as a brief explanation of the numbers, which are vibration amplitudes, in VdB, and exceedances of average plus sigma (also in VdB), at shaft rotational rate frequency.
Rotational rate frequency (1x) vibration is often simple to comprehend and detect in a spectral signature. However, the variety of mechanical fault diagnoses indicated by abnormally high level 1x vibration can make it difficult to determine what the actual problem is.
For example, consider a direct drive motor and centrifugal pump with a coupling. Excessive 1x vibration may indicate the following:
- Motor imbalance
- Pump imbalance
- Angular misalignment
- Foundation horizontal flexibility
- A radial or thrust bearing clearance problem
- Motor cooling fan blade damage
It is our analysts’ experience that collecting triaxial data at both the motor and pump is essential to diagnose and differentiate among these faults.
The following examples illustrate a variety of 1x diagnoses and the logic by which the results were obtained manually and with Azima AI powered automated diagnostic system.
Each example represents survey test data taken from motor-driven centrifugal pumps aboard U.S. Navy aircraft carriers.
Although test data included two frequency ranges of continuous spectra and forcing frequencies, the 1x amplitudes and deviations from average plus sigma have been extracted and summarized in Table 1.
Example #1: Motor Imbalance
This configuration is a vertical motor-driven pump with one transducer mounting disk on the upper motor bearing and one on the upper pump bearing. All else being equal, we can generalize that the horizontal 1x vibration levels should be roughly twice as high (6 VdB higher) at the motor than the pump due to the cantilever effect.
This relationship should be reflected in the average data.
Another physical consideration for a vertical machine is that any rotor imbalance can cause the whole unit to rock. The rocking motion can cause 1x axial vibration to be abnormally high as long as the average axial amplitudes and exceedances are lower than those for radial and tangential.
A third consideration is that vertical pumps usually are structured with one face of the coupling and upper pump bearing exposed, so that the axis of structural support flexibility allows the unit to vibrate in that direction, while the perpendicular axis is much stiffer and only allows more localized vibration.
Given these physical factors, examine the data for Example #1 in Table 1. Assume that we have only axial and radial data at both ends. The diagnosis could be angular misalignment, since 1x axial is abnormally high at both motor and pump. It could be motor imbalance or pump imbalance, since 1x radial is abnormally high at either end and radial is higher than axial. The axial vibration could be due to the rocking motion.
If we have only axial and tangential data at both ends, the evidence points more to motor imbalance, since 1x radial at the pump is quite low. With all three axes, it becomes clear that the 1x radial and tangential levels at the motor are dominant over axial in both absolute amplitude and relative to average. This indicates motor imbalance.
The 1x levels at the pump can be explained by the horizontal structural stiffness mentioned earlier. The radial axis in this case is the direction of structural flexibility, so that radially motor imbalance is “wagging” the pump. Conversely, the tangential axis is the direction of high structural stiffness and therefore the vibration due to motor imbalance does not transmit to the pump.
Example #2: Pump Imbalance
Using the same logic in example #1 and considering the same physical factors for a vertical motor- driven pump, it is evident that the data indicate either motor imbalance or pump imbalance.
The 1x radial and tangential levels are much higher than axial in absolute amplitude and relative to average at the motor and pump. Which component is more likely at fault? The 1x radial and tangential amplitudes are higher at the motor, but remember that this is a vertical machine. Amplitudes at the motor are only 2 and 4 VdB higher than those at the pump, much less than a factor of two. Furthermore, the exceedances of average in the radial and tangential axes are 1 and 7 VdB greater at the pump.
The diagnostic software concludes that there is imbalance present due to the relatively low axial levels. But ultimately, the diagnostic system will conclude the imbalance originates from the pump and not the motor because the radial and tangential exceedances of average at 1x, taken together, are significantly greater at the pump than at the motor.
Example #3: Angular Misalignment
Assume that we have only axial and radial vibration at both ends. This could be due to angular misalignment, motor imbalance, or pump imbalance. The latter could be concluded because this is a vertical machine, and the rocking motion of the whole unit can cause 1x axial vibration to be abnormally high as long as the axial amplitudes and exceedances of average are lower than those for radial.
We see abnormally high axial 1x vibration at both ends, suggesting misalignment although missing the radial amplitude that is 17 VdB (a factor of 7) higher than axial. Having all three axes provides a clear picture.
Azima’s diagnostic software notes, as would the human analyst, that the 1x axial vibration levels are abnormally high at both ends of the machine and that the axial amplitude is greater than either the radial or tangential amplitude at both ends. This information alone is sufficient to diagnose angular misalignment.
Motor or pump imbalance diagnoses require that both radial and tangential 1x amplitudes be greater than axial at either end of the machine. Since this is a vertical pump, it is structurally much less stiff in one horizontal direction than the other, and angular misalignment will often cause the machine structure to respond by “wagging” strongly in the less stiff direction.
Thus we see the 1x radial vibration levels (radial, in this case, being the structurally limber direction) are not only abnormally high but dominate the spectra. The analysis software requires the axial 1x vibration meet the appropriate rules for the angular misalignment diagnosis to pass. It uses the 1x radial or tangential levels as supporting evidence so that these peaks are included in the diagnostic report and more importantly, add to the fault severity computation. In this case, including the radial levels increases the severity from moderate to serious.
Example #4: Damaged Foundation
Assume that we have only axial and radial vibration at both ends. There is no indicated mechanical fault. All 1x levels are well below average.
It’s easy to assume that there is a moderate degree of either motor imbalance or pump imbalance. In fact, the data shown in Table 1 indicate foundation transverse flexibility.
The diagnostic software examines the differentials in both amplitude and deviation from average between radial and tangential. Although it is often normal for a horizontal machine to have tangential 1x vibration significantly higher in amplitude than radial, this characteristic would be evident in the average data. The fact that 1x tangential levels at both ends of the unit are 21 and 28 VdB higher in amplitude, and 16 and 18 VdB higher relative to average than the radial levels, is direct evidence of the foundation flexibility. The foundation is probably corroded or has a cracked weld or loose bolts.
Example #5: Bent Shaft or Two Simultaneous Issues
For this horizontal machine, it appears that angular misalignment and motor imbalance are indicated simultaneously.
1x axial vibration is abnormally high at both ends of the unit, indicating angular misalignment. Plus, the amplitude is greater than both radial and tangential at the pump and equal to radial at the motor. 1x radial and tangential vibration at the motor are 26 and 22 VdB (up to a factor of twenty) greater than average plus sigma, indicating motor imbalance. Tangential is much higher in amplitude than axial while the radial amplitude is at least equal to axial. It is the equal amplitudes of axial and radial at the motor that form a borderline in the diagnostic software.
In this case, both diagnoses are automatically produced. In fact, either of these faults independently exist or the motor shaft is bent. A bent shaft would produce indications of motor imbalance and angular misalignment. This test could be followed up by measuring the phase angles of the 1x vibration in each axis, measuring the shaft for runout and checking the alignment at the coupling.
Example #6: Motor Imbalance and Pump End Flexibility
The high 1x radial and tangential levels at the motor, both 120 VdB, are clearly excessive and dominant over axial and indicate motor imbalance. The 1x tangential level at the pump is also very high, both in amplitude and exceedance of average, but the radial level is quite low.
Similar to the horizontal machine in Example #4, the pump end shows evidence of pump transverse mounting flexibility. In this case, the vibration caused by the motor imbalance is exciting the flexibility at the pump end, indicating this independent fault. Without triaxial data, it would be impossible to diagnose these two independent issues.
Example #7: Pump Rotor Imbalance
The case is similar to Example #4, only more serious, since the tangential 1x vibration is dominant.
Having both radial and tangential data allows comparison of the radial 1x data at both ends of the unit. This indicates that while the foundation transverse flexibility is clearly the problem, there is an underlying pump rotor imbalance that is forcing the inherent structural weakness to respond more severely. Without data for all three axes, it wouldn’t be possible to draw this conclusion.
Example #8: Motor Imbalance in Rotor
For close-coupled pumps, high 1x radial and tangential levels and relatively low axial generally indicate motor imbalance, as the motor rotor is supported at each end by bearings. On the other hand, a significant axial component to the 1x vibration in addition to abnormally high 1x radial and/or tangential indicates an imbalance of the overhung pump rotor.
In this case, radial and tangential 1x levels are much higher than axial in absolute terms and relative to average. Therefore, this diagnosis is motor imbalance.
Example #9: Pump Imbalance in Rotor
Refer to Example #8. In this case, axial and tangential 1x levels are much higher than radial in absolute terms and relative to average. Thus, this diagnosis is pump imbalance, as the pump rotor was physically rocking on the shaft.
Don’t forget, it’s not always accurate to assume for every machine of this configuration that the axial and radial axes are the most critical, while the tangential axis can be disregarded. In numerous instances, an imbalance in a fan or pump is signified solely by significant axial and tangential 1x vibration (or sometimes it involves all three axes).
The Power of Triaxial Data in Machine Diagnostics
Collecting triaxial data provides a much clearer picture of machine health than relying on single-axis measurements. By capturing vibration in three directions—axial, radial, and tangential—maintenance teams can differentiate between common faults like imbalance, misalignment, and structural flexibility with greater accuracy.
The case studies illustrate how having all three axes of data removes ambiguity, allowing for precise diagnoses that would be difficult or impossible with limited data. Whether dealing with a simple motor imbalance or a complex combination of faults, triaxial vibration analysis enhances diagnostic confidence, speeds up decision-making, and ultimately improves machine reliability.
By leveraging advanced analytics and AI-powered tools offered by Azima’s condition monitoring solution, teams can transform vast amounts of vibration data into actionable insights—keeping operations running smoothly and minimizing costly downtime.
For more information on Azima’s triaxial sensors, click here.
Author bio: Bill Watts Senior Vibration Engineer at Azima DLI
This piece has been updated for accuracy and clarity.