If you work in industrial maintenance, you already know that a false alarm can be just as dangerous as a missed alert. As plants increasingly adopt installed vibration monitoring systems (with a wide range of wireless sensors and monitoring systems now available on the market), the automation of vibration analysis and the potential for getting an overwhelming amount of false or nuisance alerts is causing problems. This phenomenon, known as “crying wolf,” doesn’t just waste time; it erodes trust in monitoring systems, leading to potential oversight of genuine issues.
So how do you overcome this challenge?
Advanced vibration monitoring solutions are stepping up to help by providing precise, timely alerts necessary to maintain operational efficiency and avoid false alarms.
In this article, Michael DeMaria, director of product management at Fluke Reliability explains how advanced vibration sensors and artificial intelligence-powered diagnostic technology are cutting through the noise and transforming asset maintenance for the better.
But first, let’s dive into the problems that make this technology necessary.
The Promise and Challenge of Wireless Vibration Monitoring
Today, wireless vibration sensors are standard in industrial settings. However, while these devices offer unprecedented convenience and flexibility, they also pose significant challenges.
One of the most pressing issues is the boy-who-cries-wolf scenario. This happens when a machine falsely alerts technicians to a breakdown or maintenance need, even though the machine is operating like normal.
Several factors contribute to this issue. Inconsistent data quality, machines operating outside normal operating parameters, assets going through a start-up/shutdown, and faults that are just on the edge of needing action, can all lead to frequent false alarms that overwhelm maintenance teams, making it difficult to discern which alerts are truly critical.
Exploring the Depth of the Problem
The causes of false alarms are deeply interwoven, involving not only the data collection process but also the management and interpretation of data. Here are the main reasons why they occur:
- Low Data Quality
The quality of data captured by sensors can sometimes play a role in causing false alarms. DeMaria emphasizes the issues with low-quality data, explaining that, “[It] doesn’t help us. It’s just more monitoring of the machine and less information.” With these kinds of readings, databases become cluttered with data that doesn’t provide enough insight to know when a machine really breaks down.One contributing factor to low-quality data is capturing information during non-representative machine states, such as startup cycles. As DeMaria explains, “If the sensor captures data during a startup cycle, it’s not useful information. We can’t utilize that data effectively, leading to nuisance alarms. It results in no clear actionable steps we can take.”
- Inconsistency in Data Capture
As machines operate under variable conditions, it can be difficult to capture consistent and reliable data. “You have variable speed machines. They’re running at different parameters. You have conditions where things are just constantly changing,” DeMaria notes. This inconsistency can lead to unreliable information.
- Managing Data Overload
Additionally, many reliability professionals face challenges with the excessive volume of data captured by sensors. DeMaria explains, “The amount of data people are capturing is growing at an enormous rate, but we’re not using most of it. More data does not necessarily mean better results just because we’re capturing more and more data. It’s not necessarily giving us any more useful information.”Studies show only about 2% of the captured data is actually being utilized, and even then, it’s often after an event has occurred says DeMaria. “Usually, it’s waiting for a machine to fail so that you can train a system that identifies the reason for failure and just hope that the machine’s going to fail the same way a second time. But that is not usually the case,” he explains. “A bearing can fail in a number of different ways. A machine can fail in a number of different ways. So you can’t just wait for a fault to occur, have that expense of failure, and just hope that it’s going to find it the same way again. There has to be a better way.”While sensor data can be vital for preventive maintenance, most data collected does not contribute to maintenance strategies or decision-making. Rather, it is analyzed reactively, which diminishes its value or merely spot-checked, making the necessity for such volumes of data moot.
- Contextualizing Data from Different Systems
Complicating things even further, using multiple devices from different vendors can lead to different alerts that are hard to interpret when looked at together.
DeMaria explains, “If I have a wireless device from one vendor, a portable system from somebody else, and I have an installed systems from yet another vendor, the information I receive at the end can seem out of context. If a wireless sensor has given me a red light, but my walk-around system is saying I have a serious problem, and my online system says I have a priority one problem, do those all mean the same thing?”
- Turning Data into Actionable Insights
Simply throwing AI-driven analytics at the problem isn’t the answer. If a system comes equipped with AI or machine learning, it can be helpful — but DeMaria notes that it does need to be trained with information to make decisions. Without trained data, the system can’t recognize patterns and draw insight that will help avoid false alarms.
Turning Noise into Nuance: The Future of Alerts
Advancements in wireless sensor technology and intelligent diagnostic systems can cut through the noise to deliver precise, actionable alerts exactly when needed. These innovations reduce false alarms and allow maintenance teams to focus on truly critical issues. Here’s how:
- Sensors That Actually Capture High-Quality Data
Advanced wireless sensors can provide the high accuracy and reliability needed for professionals to perform preventive maintenance on an asset at exactly the right time. Wireless sensors like the Azima Accel 310™, for example, use triaxial accelerometers to capture higher-quality data. consistently triggered by an is-running logic test.
- Mesh Networks Boost Coverage & Data Consistency
Mesh connectivity allows each sensor to act as a data transmission point, enhancing system coverage and reducing the dependency on extensive infrastructure. This scalability means that the system can grow with the needs of the operation, delivering a consistent over-the-air data stream to maintain reliability across larger networks.
- Integrating Data from Different Devices
To address the issue of conflicting alerts from multiple devices, some monitoring/diagnostic solutions are now able to connect and integrate wireless sensors with other predictive maintenance technologies.
Take Azima Watchman AIR, an industrial wireless vibration solution, for example; it can integrate with a range of other data collection devices such as portable, route-based or advanced, permanently-installed devices, making it suitable for all types of equipment, environments, and processes. With a solution that is easily scalable and integrates easily with reliability programs of all sizes and geographic diversity, you’ll know exactly what’s a real issue and what’s not.
- Advanced Diagnostic Systems
Automated diagnostic systems can recognize complex patterns in machine behavior, predict failures, and reduce false alarms. These systems don’t rely solely on learning from past experiences; they are trained on extensive data points that allow them to automatically identify issues and faults, accurately and reliably.
“To continue the example, a system like the Watchman AIR will take the high-quality data collected by the sensor and give you useful information automatically,” explains DeMaria. Because the Watchman diagnostic engine has been trained on 30 years of data and draws from 100 trillion data points across 50 machinery component types, it can tell you specifically what you need to do to fix a problem.
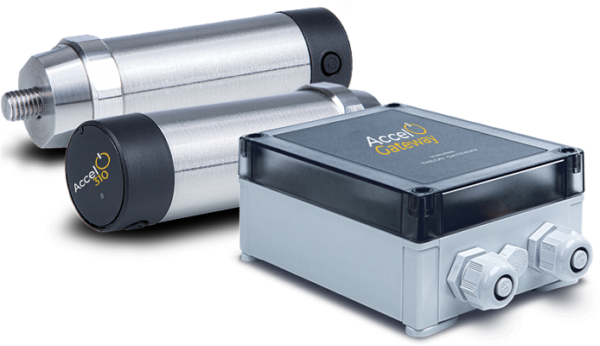
The Watchman AIR (Image credit: NPE)
Additionally, other advancements help in eliminating the crying wolf nuisance such as stability logic to ensure a fault has stabilized and not a nuisance from a machine startup, persistence logic to automate the diagnostic findings once a fault is flagged, lessening the workload on the analyst tasked with validating significant faults, and data quality filtering to identify bad data, abnormal conditions, and hardware faults as non-actionable notifications independent of prioritized, actionable repair recommendations.
What Does This Mean for You?
So, what does all this mean for you as a reliability professional? In short, less noise and more clarity. It starts with switching to wireless sensors that capture high-quality data and a sophisticated AI-powered diagnostic system that easily integrates with your existing systems. This helps in three ways:
- Ensuring reliable and consistent data capture
- Gathering high-quality data, every time
- Using intelligent diagnostics to provide specific and component-level information and repair action recommendations for each data set
All in all, by using these technologies, you can look forward to fewer false alarms and a clearer picture of your machinery’s health. You’ll be able to trust your alerts, focus on the real issues, and plan maintenance activities more effectively. No more crying wolf — just reliable data to keep your sanity intact.
Ready to cut through the noise and focus on what really matters? Let’s chat about how our advanced condition monitoring solutions can help.