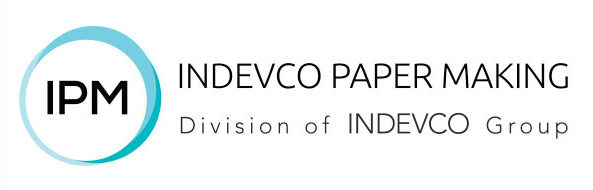
Data, Diagnostics, and Zero Catastrophic Failures in Four Years: The Azima Advantage at Interstate Paper Industries
Customer Since: 2014 | Industry: Paper
Summary
Interstate Paper Industries (IPI) doesn’t have the luxury of downtime. Running nonstop all year, the company needed a smarter way to manage machine health. By adopting the Azima predictive maintenance approach, they replaced guesswork with data-driven decisions — and the results speak for themselves:
- Zero catastrophic failures in four years – Early detection keeps operations running smoothly.
- Faster, cost-effective repairs – Planned maintenance takes half the time and avoids unnecessary expenses.
- Optimized performance with confidence – Real-time insights allow IPI to push for efficiency without risking equipment health.
Background
At Interstate Paper Industries (a member of INDEVCO Paper Making, which is a division of INDEVCO Group) the production line is always in motion. As one of Egypt’s leading tissue manufacturers, IPI produces 50,000+ metric tons each year. The company exports its products to customers across Europe, the Middle East, and Africa for use in household and commercial settings. IPI specializes in virgin and recycled tissue, supplying a fast-moving industry that relies on consistent production.
To keep up with this demand, IPI’s paper mill in Sadat City operates 24/7, 365 days a year. A facility that never stops doesn’t leave much room for unexpected breakdowns, so IPI needed a way to identify and prepare for failures before they could derail production.
Challenge
Before Azima, the IPI maintenance team had a system in place to track machine health, but the tools they used had serious limitations. The team performed daily temperature checks and relied on a basic handheld pen accelerometer to measure vibration. “It was very rudimental,” says Alexandre Akl, maintenance manager at IPI. “You could see if the vibration exceeded 3 mm/s, but it didn’t tell you if a failure was coming in the next few months.”
With no way to see gradual deterioration, IPI could only react once a problem became severe. “Before Azima, we had to wait for a big noise, look around, stop the machine, and then figure out where the issue was,” Akl recalls. That meant unexpected breakdowns at the worst possible time — on one occasion, it was at 5 a.m. when the full team wasn’t available. With key personnel off-site and the right parts not in reach, what could have been a straightforward fix turned into a prolonged repair, costing the facility uptime and profits.
IPI wanted a predictive approach that put control back in their hands — one that gave them the ability to anticipate issues and plan repairs in a careful and organized way.
Implementation
To make this shift, IPI implemented the full Azima predictive maintenance solution — an interconnected system of hardware, software, and expert service. This includes TRIO vibration analyzers for on-site data collection, the Azima diagnostic portal for advanced analysis, and a dedicated expert vibration analyst to interpret the data and provide targeted recommendations.
- High-fidelity data collection with TRIO: Each month, facility technicians collect vibration readings from 50 critical machines using TRIO vibration analyzers. These devices capture precise, high-fidelity data, which is critical because the quality of the input determines the value of the insights. “Rubbish in is rubbish out,” Akl puts it. “If the data isn’t accurate, the software can’t properly analyze vibration frequencies or detect abnormalities.” The readings — 300 data points in total — are recorded as part of IPI’s routine monitoring process, with data collected across six days each month and automatically sent to the Azima diagnostic portal.
- Artificial intelligence (AI) that spots failures before they happen: Backed by over 30 years of industrial vibration data, or more than 100 trillion data points across 50 machinery component types, the AI-powered Azima database recognizes failure patterns with unmatched accuracy. For IPI, this means faster, more reliable diagnostics. The system automatically flags abnormal patterns, pinpoints root causes, and classifies issues by severity — extreme, severe, important, or normal. With this structured approach, IPI no longer has to guess which machines need urgent attention.
- Expert analysis you can trust: Vibration analysts at Azima review every report generated by the system implemented at IPI. These specialists validate findings, identify patterns, and provide clear, prioritized maintenance recommendations. Akl values this extra layer of oversight. “The team at Azima does a good follow-up job,” he says. “If we miss something, they catch it and let us know.”
This collaborative and structured approach gives IPI the ability to plan repairs strategically, aligning interventions within their scheduled maintenance windows instead of scrambling to react to sudden failures. “It’s like having a radar,” Akl states. “You’re not just waiting for something to happen — you see it coming.”
Results
With 12 reports per machine annually, IPI moved from uncertainty to complete visibility. The team knew which bearings were degrading, which shafts were misaligned, and which machines needed attention first during their scheduled shutdowns.
Over the past decade, the results have been undeniable.
Four years without a major failure: “Every month, we diagnose one or two machines with failing components before they break down,” Akl says. “We no longer wait for the emergency — we act before it happens.” Four years without catastrophic failure is proof that early detection has turned maintenance into a controlled, strategic process. “That’s how effective this system has been,” Akl says.
Lower repair costs, less downtime: Unplanned failures take twice the amount of time to repair and cost twice as much as scheduled maintenance, Akl explains. “Some bearings are $6,000, $7,000 … and we’re talking about big shafts; 4.5-meter diameter, 70-ton cylinders. Replacing a bearing takes a full day, including stopping, cooling down, and installation. But if technicians don’t diagnose the issue in time, the damage can spread to the main shaft, which is an even bigger problem. Repairs take far longer and cost much more.” With failures now caught early, IPI can avoid these costly, last-minute repairs and plan maintenance around production — not the other way around.
For instance, the team experienced a similar failure in the forming roll that previously took eight hours to repair. “After Azima, the same failure took just four hours because we were prepared,” says Akl. “And even better, we did it during a scheduled shutdown.”
Maximizing performance without risk: Before, without full visibility into equipment conditions, increasing machine speed carried risks. “How do you know if you can go up to a higher speed if you don’t really know if you have vibration or not?” says Akl. But now, with real-time insights, the IPI team can push for higher efficiency without second-guessing machine health.
For Akl, it’s about more than just keeping the machines running. Azima gives his team confidence in every decision. “You know, we run 24/7, 365 days a year. So how can you optimize productivity if you don’t really know the status of your equipment?” he asks. “It’s like running an ECG. You don’t wait for a heart attack — you check regularly.” With continuous monitoring guiding their decisions, IPI can increase speed strategically and safely — making every production hour count.
Increased uptime, increased profit: Azima enabled fewer failures, faster repairs, and lower costs at IPI. And the impact? Akl describes it simply: “Less downtime is more uptime, more uptime is more productivity, more productivity is more profit. That’s how it’s done.”
A Decade of Smarter Maintenance
Ten years ago, IPI’s maintenance team had to listen for a big noise before they knew something was wrong. Today, they catch failures before they make a sound. Every decision is backed by data, repairs are planned in advance, and all machines run with the guarantee that they’ll keep producing as long as possible. “We’re not just using a product — it’s a program, a way of doing maintenance that actually delivers results,” Akl says.