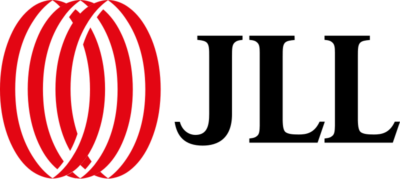
How Azima DLI and JLL Drive Predictive Maintenance in Facility Management
Industry: Real Estate
A leading real estate management firm harnessed the power of Azima DLI to deliver greater uptime and efficiency to its customers.
Summary
Jones Lang LaSalle Incorporated, or JLL, is a commercial real estate management firm. Maintenance is at the heart of everything the company does, and the maintenance, repair, and operations (MRO) team is always looking for more effective approaches for monitoring and repairing equipment.
JLL first used one Azima TRIO vibration analyzer and AI-powered diagnostic engine at a single site. After seeing positive results, they expanded its use across five of the facilities it manages, resulting in:
- Reduced equipment downtime
- Up to tens of thousands of dollars per day in cost reductions
- Increased operational efficiency thanks to Azima’s intuitive technology
- Early diagnosis of machine faults
- Smoother scheduling, forecasting, and budgeting processes for JLL and its customers
Background
Jones Lang LaSalle Incorporated is a Fortune 500 company that provides commercial real estate management services. Headquartered in Chicago, Illinois, JLL has offices in 80 countries. Its clients include small startups as well as global leaders in sectors like banking, energy, life sciences, manufacturing, and technology.
JLL offers a full range of property management services, including building and facility management solutions. Its MRO teams are responsible for keeping highly sensitive sites like power plants and biomedical facilities in top working order. In addition, the team also maintains hotels, stores, and other commercial sites.
Challenge
JLL manages 4.6 billion square feet of property around the world. Implementing change across such a huge area is a major challenge, and the company needed a solution that was scalable and customizable for different facilities.
Ken Snyder, a senior reliability director at JLL, saw an opportunity to boost efficiency and reduce downtime by implementing a proactive, data-driven maintenance strategy. However, the implementation process posed some challenges. Snyder said that, at many of the sites JLL manages, teams were struggling to implement a predictive maintenance (PdM) program.
Implementing a traditional PdM program would require large-scale training and hiring more technicians to analyze huge quantities of condition monitoring data. JLL wanted to find a software solution that could analyze vibration data with minimal human supervision to keep costs low without sacrificing results.
Having worked with vibration analysis tools for decades, Snyder knew exactly what to look for in a system.
He’s spent 39 years as a vibration analyst, reporting on equipment from power utility, chemical manufacturing plants to pharma research facilities. Early in his career, he primarily used Bently Nevada vibration analysis equipment to monitor powerhouses but when he came across Azima DLI Engineering, he immediately saw its potential. He even visited Bainbridge Island to meet the team behind the technology and see firsthand how it was developed. By the time he transitioned into big pharma, Azima had become his go-to—and it’s remained his trusted solution ever since.
So, when it came time to find the right predictive maintenance system for JLL, he knew that Azima’s “brilliant” diagnostic capabilities, ease of use, and intuitive interface made it the clear choice.
And the results spoke for themselves. By harnessing the power of Azima AI, JLL was able to speed up its diagnostic process and repair emerging asset faults quickly. The company was able to deliver greater uptime and pass along savings to customers.
Implementation
Snyder started working closely with five of JLL’s corporate customers to implement the new PdM program with Azima. He provided each customer with a TRIO vibration analyzer and trained their teams to take vibration readings and sync the data to the cloud.
Using the TRIO Vibration Analyzer
Snyder offered customers the choice to either lease or buy the TRIO devices. Some customers chose to use one TRIO and rotate it between their different facilities. Other companies acquired more than one TRIO.
Workers at each facility used the TRIO to measure vibration levels on assets throughout the worksite. The TRIO devices are designed to be simple to use, even for inexperienced employees, which makes implementation easy.
In fact, Snyder snapped a photo of his team on day one of the implementation process, shortly after he handed them the TRIO devices. The crew was comfortable with the technology after just a short run-through. As Snyder pointed out, “Guys are teaching other guys how to use it – that’s how easy the box is to use.”
AI-Powered Diagnostic Tools
Snyder’s crew streamed machine data to the cloud, where Azima’s diagnostic engine analyzed it and created a detailed report listing any new and emerging machine defects. The reports included health ratings for each asset in the facility, along with step-by-step recommendations for maintenance teams to follow.
At JLL, Snyder takes the Azima reports and makes sure they’re put into action. He reads the analysis and uses it to pinpoint exactly where maintenance crews should be putting their time and resources. So far, the combination of AI diagnostics and human intervention is making a big difference to JLL’s customers.
Snyder said the software has helped catch machine faults at the earliest possible stages. That’s thanks to Azima’s use of logarithmic scale – a feature that makes it easy to identify even subtle changes in an asset’s vibration frequency.
“The logarithmic scale brings everything up from the floor, so you can see it,” Snyder said. “That’s the home run. That’s the Holy Grail right there.”
Results
Azima tools saved one of JLL’s customers, a cogeneration power plant, tens of thousands of dollars in just one day.
Abnormally high vibration readings indicated that there was an issue with one of the plant’s vertical boiler feed pumps. The motor attached to the pump started running at 3600 RPM instead of its usual 2600 RPM after its variable frequency drive (VFD) tripped.
Snyder and his team collected data from the pump with a TRIO and used Azima’s ExpertALERT Diagnostic Software to analyze the data. Azima was able to diagnose the root cause of the change in vibration levels, indicating that one particular coupling had loosened. The software indicated that this was a severe fault that needed immediate attention.
Teams went out to inspect and found that half the coupling was missing. They were able to make repairs quickly and get the pump running again right away. The next day, the pump and motor were once again in good condition.
Snyder estimated that by pinpointing the coupling fault, Azima saved the plant at least $36,000. Without Azima’s diagnostics, crews would have needed to take the motor off of the pump (at an estimated cost of $10,000), replace the bolts, and rebuild the entire base. That estimate doesn’t account for the cost of potential downtime if the motor and pump had failed.
Next Steps
JLL plans to expand its use of Azima so that more of its customers have access to the diagnostic tools. The company is interested in offering access to Azima’s wireless sensors as well as the handheld TRIO devices.
Looking ahead, as more customers onboard the new tools, JLL will likely tap into the deep bench of vibration experts at Fluke and Azima. Those experts analyze Azima’s findings and work closely with maintenance teams to implement the correct response. They can also provide training, help with troubleshooting, and perform remote condition monitoring for facilities around the world.
With this support, more JLL-managed facilities are adopting a predictive maintenance strategy that prioritizes efficiency and reliability. ‘We’re going to be building it out even more,’ Snyder added. ‘People love this thing.’
For Snyder, seeing this shift is a full-circle moment. After decades of relying on Azima’s technology himself, he’s proud to see it continue to set the standard, stating Azima is the best vibration analysis company available today.”