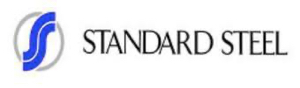
Within a Month, Azima DLI Prevents Three Asset Failures at Standard Steel
Customer Since: 2024 | Industry: Railroad Equipment Manufacturing
Azima’s AI-powered vibration analytics and condition monitoring solution provided a cost-effective, rapid intervention, preventing three equipment breakdowns at Standard Steel and maintaining production continuity.
Background
Standard Steel is a leading manufacturer of forged steel wheels and axles for locomotives and railcars used in freight and passenger trains. The company is also the only producer of forged steel wheels for railcars and locomotives in North America , serving major Class I railroads, railcar builders, maintenance shops, locomotive builders, and national and regional transit authorities, like Amtrak.
The company relies on over 300 critical assets to maintain operational efficiency and minimize downtime, contributing to uninterrupted production and high-quality output for its prestigious customers.
Challenges
Standard Steel faced two main issues with its previous vibration analysis vendor: high costs and the need for better value, which prompted the company to re-evaluate its options. To address this issue, the company sought a more cost-effective and reliable solution that could provide better data to improve maintenance outcomes.
With Azima providing more accurate data at a lower cost, Standard Steel knew it was the right move.
Implementation
The Azima team didn’t just install the vibration sensors and a diagnostic system at the facility’s wheel mill — they made the entire process informational and insightful for the Standard Steel team. “They were very good at showing me, who knew nothing about vibrations, exactly what to look for in the predictive portal system,” says Andrew Boyer, a maintenance & reliability engineer for Standard Steel. “They didn’t just install — they were showing me exactly how it works, which helped me greatly in reading and understanding the data.”
With this thorough training, the Standard Steel team was ready to use the new system immediately.
Results
The impact of Azima’s condition monitoring solution at Standard Steel became quickly and dramatically evident. Within a month, Azima’s wireless vibration sensors prevented failures in pumps and motors for three critical assets essential to Standard Steel’s production line.
- Crisis averted on wheel metal production line: “One of the assets saved was a wheel press boost pump”, explains Boyer. “If it had failed, we would have lost our entire wheel mill production line. But the sensors identified that a bearing was locking, and we got there and checked it to see that one of the external bearings was starting to lock up.”
- Motor malfunction prevented: Another critical save involved a motor with alarmingly high vibration levels. A sensor indicated that there was an issue, and the team got right to work. “When we checked it, there was no question about the vibration levels; they were clearly higher,” Boyer says. “There are three pumps in the series there, and compared to the others, this one had much more vibration, which we could physically see.”
Azima’s advanced technology was built to catch close calls before they turn into all-out disasters. For Standard Steel, the results were immediate. That’s all thanks to the system’s out-of-the box capabilities, which include:
- Advanced sensor capabilities: As Azima’s wireless vibration sensors are designed to collect three channels of vibration data simultaneously, they provide more accurate and comprehensive data. Triaxial architecture and heat-sensing technology made Azima sensors a preference for Standard Steel’s tracking program, Boyer says.
- Durability: The robustness of Azima’s sensors was another advantage. “One sensor held up a 500-pound motor like a kickstand, and it’s still reading just fine. And that’s how you know it’s truly durable. Our motto around here is that if a piece of equipment can survive at Standard Steel, it’ll live anywhere because we are not gentle on anything,” Boyer quips.
- Accurate diagnostics: Azima’s AI-powered diagnostic engine is trained on 30 years of data, drawing from 100 trillion data points across 50 machinery component types. This breadth and depth means that the system can accurately detect anomalies in most equipment functionality and alert maintenance and reliability professionals when issues are detected — just as it did for Standard Steel. “The system has been pretty spot-on,” Boyer emphasizes. “I really like how accurate the predictions actually are.”
- Ease of use: The analytics platform’s user-friendly design makes it easy for even non-specialists to navigate and understand. “[It] is a lot easier to navigate than [Azima’s] competitor that we were using previously,” says Boyer. “I’m no vibration specialist, but this is simple enough that I can read it and understand what’s happening.”
- Better preventive maintenance scheduling: Azima sensors provide timely alerts, allowing process engineers to schedule maintenance proactively and strategically using eMaint scheduling software in order to avert a crisis. At Standard Steel, this means the team can do impactful work during scheduled maintenance shifts, rather than during unplanned downtime. Boyer says the process helps facilitate better planning.
Next Steps
Looking ahead, Standard Steel plans to expand its use of Azima’s technology beyond the wheel mill, thanks to its affordability and the ease of use of the sensors, which means that there won’t be a steep learning curve for staff at other locations. “That’s our goal—to collect more data and move towards a proactive maintenance plan rather than a reactive one,” Boyer explained.